Two stoke engines of MAN
By Ferdinand Brandes
Machine translated by Google
Experiences of the former German Navy in the development of high-speed speedboat engines and the double-acting two-stroke engines of MAN
Preliminary remark
Ferdinand Brandes worked until 1944 as a ministerial director in the design office of the German Navy, in a position comparable to that of chief mechanical engineer in the design office of the Imperial Navy. In this position he had a significant influence on the mechanical engineering development of German warship construction. He was a long-standing member of the Shipbuilding Technical Society. After his death in 1974, his wife Hertha became a member of the society and regularly invited the board of the society to Bad Salzuflen. Prof. Keil accepted these invitations, to which various former naval construction officials were also invited. After her death in 2005, I was given the draft of a report from Mrs. Brandes' estate, which Ferdinand Brandes had prepared for the Blank office in 1955, for free use. Since this report was only available in part as a fragment with many handwritten changes and the whereabouts of the original is unknown, it required editorial processing.
Now that, after almost 60 years, there are extensive studies on the engine developments described by Brandes1 and most of the facts are documented using many documents that Brandes, as a private citizen, had only partial access to in 1955, the value of this work seems to me to lie in the fact that a direct contemporary witness has described the development. Publishing this document is the best way to do justice to the work of Ferdinand Brandes and the naval construction officials involved. Thankfully, Hans-Jürgen Reuß, who is well known for his several publications on the development of the diesel engine, proofread the manuscript and provided various information to clarify the situation.
Eike Lehmann
Introduction
If we want to report here on experiences from the engine sector of the former German Navy, then that means mentally replaying a development period of almost 20 years in chronological order. A period in which it was possible to develop marine engines from small beginnings to a high level. With the end and destruction of the German Reich, this period also came to an end.
Ten years have passed since then; but time does not stand still and has not stood still now either; it has changed and with it people, their thoughts and ideas. The old saying: "Tempora mutantur et nos mutamur in illis" 2 has proven true here in a short space of time and in a way that is rarely seen before. How else could it be that after these ten years, at the beginning of which all means were justified in striking the former German Wehrmacht to the core, the same peoples are now raising their voices and calling for the rearmament of the German people and the reconstruction of a defense force It is therefore understandable that those now called upon to rebuild should look around to see where useful building blocks can still be found in the rubble of the former German Reich: building blocks that can form a foundation and the beginning of the first work of a new armed forces.
These building blocks are indispensable. They are the experiences of the past, which were gained through hard work over the course of many years and at enormous financial sacrifices. The intellectual work that has been done in the area to be dealt with here and which extends over several decades cannot be described in its entirety in words and figures; only the most important results of this development work, the most valuable experiences, can be reproduced. "Experience is a collection of human stupidity," as a member of the Bundestag recently said in a speech on the rearmament of the German people. And stupid things that have happened should not be repeated. This requires taking into account and applying the valuable experiences gained through hard work. But where can these experiences be found and collected today, after authorities and industrial plants have been plundered and all technical designs, construction drawings and building regulations have been carried away and the employees in this field have been scattered to the four winds?
are looking for new areas of work and activities. So the only way left is to contact one or another of the few surviving or reachable employees in the field under discussion here who experienced or even influenced the development of motor drive types and can look back on a long series of years of experience.
If I have now been given the task by the "Commissioner of the Federal Chancellery"3 to write down the experiences of the former Navy in developing high-speed S-boat engines and the double-acting two-stroke engines of the MAN, this can only be possible by painstakingly compiling the past from memory in words and sketches, as, as already mentioned, the industrial plants were robbed of almost all technical documents and experience in this field by the collapse of the Reich and its consequences. After all, one of the Western war aims was to destroy the German economy. If the following treatment is to be of real value, it must not contain fiction and truth, but must convey soberly and unvarnished all the experiences and knowledge that led to a certain peak in the motor drive systems of military vehicles by the end of the war.
Fast boat engines
Maybach engines
When describing the development history and the experience gained from speedboat engines, which began at the end of the 1920s and which I witnessed and influenced as a direct participant from 1933 onwards, it would be correct to also mention the first speedboats of the Imperial Navy from the war years 1916 to 1918, whose Otto engines were not built as speedboat engines, but for the first time ever made it possible to build speedboats.4 These were Maybach engines intended for Zeppelin airships, which had been approved by the aviation industry because it was switching to an improved new type of engine.5 The boatyards of Fr. Lürssen in Vegesack, the Rolandwerft Vertens & Co. Hemelingen and the Oertz Werft in Hamburg-Neuhof were commissioned to build the boats. The boats, which had a torpedo tube half-embedded in the foredeck, ran with three of these Maybach engines at a maximum speed of about 30 knots for a short time. The data of these engines of the Mb IVa6 type were: 240 hp normal, speed 1300–1400 rpm, weight about 1.7 kg per hp. The length of the boats was 16 m, the width 2.4 m and the side height 1.3 m. The water displacement was about 7.8 t. These Maybach engines, which were not reversible, had no reversing gear and no adjustable pitch propeller, only had a lamella coupling, also adopted from airship construction, for switching the engines on and off. The idea of having a vehicle with a non-reversing propeller was initially met with little military approval. However, since a light reversing gear suitable for these boats would have taken far too long to develop at the time, the choice was: S-boats of the type specified or none at all. The boats were built and it turned out that with skillful maneuvering, all docking and undocking maneuvers could still be carried out without great difficulty. When designing these boats, the speed of the engines – 1300–1400 per minute – was another stumbling block, as this speed had to be transferred to the propeller due to the lack of a reduction gear.7 The Navy, which at the time had no experience with such high propeller speeds, benefited from the experience of the Lürssen boatyard with its racing boats at the international races in Monaco, so that no difficulties arose due to these high speeds. The Navy had little joy with these air engines, however; there were always problems, not that any one part failed in particular. In general, they were too sensitive to be used as boat engines. I would like to remind you of the embarrassing incident, the accident involving the Zeppelin airship, which had to make an emergency landing on French soil because all the engines broke down one after the other. As far as I can remember, the investigation into the cause of this mishap revealed that they were based on Overstressing the crankshaft caused by torsional vibrations that were not recognized or not yet detectable at the time. To my knowledge, however, a shaft break due to torsional vibrations never occurred on board the speedboats; the weaknesses or faults that existed earlier had probably been eliminated in these engines. I can write this historical review of these first speedboats in such detail because, as a consultant in the ReichsNaval Office at the time, I witnessed everything and personally arranged it. There is probably hardly anyone else left who can provide information about this period of the first S-boats. The experience with these Maybach engines, which were certainly a very significant achievement in lightweight construction for the time, can be summed up as follows: speedboats require their own engines that have to be very stable and robust even with an extremely low weight per horsepower.
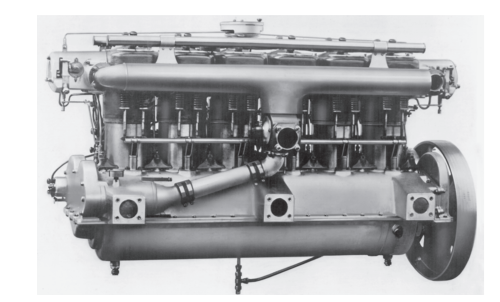
Junkers engine
The Junkers works, which were also geared towards lightweight construction through their aircraft production, were also called upon to build a speedboat engine that was designed using the opposed piston system. It was a petrol engine with injected fuel. It had six horizontal cylinders with opposing pistons and two crankshafts on the sides that transmitted their torque to the propeller shaft via gears. At 2300 rpm it was supposed to produce 660 hp. With a reversing gear it weighed 1070 kg. Towards the end of the war this engine was ready to begin its test runs on the test bench. However, it soon became apparent that the calculated power was far from being achieved. The noise generated when the engine was running was also simply unbearable. The end of the war also meant the end of this engine.

Siemens and Körting engines
Two other types of speedboat engines from Siemens and Körting never got beyond the first test cylinders. At the end of the 1920s, the naval leadership decided to design special engines for speedboats and awarded the Daimler-Benz works in Untertürkheim near Stuttgart, and MAN in Augsburg the contract for design and construction.
Speedboat engines from Daimler-Benz
Based on their experience in car engine construction, the Daimler-Benz works in Stuttgart initially supplied turbocharged petrol engines for the LM 20, 22, 23 and 28 boats. The boats initially ran under cover names with "civilian" crews and were unarmed. Three boats received 3 x 260 hp engines, two boats 1 x 260 hp on the middle shaft, 2 x 210 hp on the outer shafts. Since after these boats petrol engines were basically no longer to be used on speedboats,
Daimler-Benz developed the next type of speedboat engine, a 2 x 6-cylinder V-shaped diesel engine type MB 500, which had an output of 950 hp at 1630 rpm. Cylinder diameter 175 mm, stroke = 230 mm. A reduction gear of 1.72:1 was attached directly to the engine. The speed of the propeller shaft was therefore 950 rpm. This engine was soon followed by another with the same dimensions (type MB 502), but with 2 x 8 cylinders and an output of 1320 hp. The crankshaft bearings, which were designed as roller bearings, caused great difficulties with this engine. Since, despite several changes and extensive tests, a fully satisfactory running of these roller bearings could not be achieved, it was decided to abandon these roller bearings and to design them as plain bearings. In this form, the bearings ran to complete satisfaction in both the 16-cylinder engine and later in the 20-cylinder engine MB 501.8
Both engine types, which initially had no turbocharging, were given turbocharging in the engine types MB 511 and 512 and as such were installed in large numbers in the naval speedboats. The 20-cylinder engine with a mechanically driven turbocharger with a cylinder diameter of 185 mm and a stroke of 250 mm at 1630 rpm produced around 2500 hp. After the problems with the roller bearings of the pin bearings had already been resolved in the types MB 502 and MB 501, cracks appeared in the welded cooling jackets of the cylinders in the types MB 511 and 512, which could only be repaired over time. The injection nozzles on the pre-chambers also caused problems. They cracked or came off, causing mechanical damage and also burning or even burning through of pistons. These defects were later remedied by choosing more suitable materials. Experiments with turbochargers on these engine types were unsuccessful.
The front's demand for ever greater speed also required increased engine performance. Before the end of the war, an engine type with 3000 HP at 1730 rpm had been installed in a boat after some difficulties on the test bench. It had a bore of 185 mm, and a stroke of 250 mm. As with the earlier engines, the reduction gear (1.72:1) was attached directly to the engine. The propeller shaft therefore made 1000 revolutions per minute. This engine had the same layout and the same displacement as its predecessor, but was simplified in some respects and made suitable for higher speeds by reducing the rotating and oscillating masses.
The difficulties that arose in developing this type of engine lay in the correct design of the pistons and in choosing the most suitable piston material. The pistons seized and the piston material began to flow because the temperatures in the cylinder were so high that the material began to soften. The weight of the engine including the gearbox was 4600 kg. Even if, as already mentioned, some of these engines were installed on board, it cannot be said that this engine - it was called the MB 518 - with this power was already fully ready for on-board use at that time.9 This would have had to be proven through longer front-line experience. However, the outcome of the war did not allow this to happen. As the Daimler-Benz company told me in response to my request for further work on this engine, development of this engine was continued when orders for this type of engine were received from abroad. The piston problems were thus eliminated by developing a completely new combustion process. A whole series of other improvements were also made, so that today (1955) this engine can be considered ready for on-board use with 3000 hp and 1720 rpm. The fact that soon after the end of the war in 1945, foreign countries ordered German speedboat engines of the above type is proof of the recognition of the quality of German engines and at the same time of the correctness of the path taken by the German Navy. If the newly formed German Navy also decides to build S-boats, I believe that this engine will initially be the most suitable German propulsion engine.10
Speedboat propeller
In connection with the speedboat engine, it is essential to point out the correct dimensioning and design of the propeller, which caused great difficulties and required, in addition to repeated towing tests, great experience and a fine feeling for avoiding cavitation phenomena.
Unfortunately, the valuable knowledge and experience in this specialist field also went into the grave with Ministerial Counsellor Heinrich Schmidt, who died in 1955.11 When building new speedboats by the newly established German Navy, special attention must be paid to the S-boat propeller and it must be remembered that it must work as economically and cavitation-free as possible both for the boat's maximum speed and for low speeds and at the same time be in line with the power and speed of the engine. The importance that the former Navy attached to a flawless propeller can be seen from the fact that, due to repeated difficulties, a special propeller commission was formed to determine the most suitable propeller, which included representatives from the university and the towing test institute.
MAN speedboat engine
While, as shown, Daimler-Benz developed a 4-stroke engine in V-shape as an S-boat engine, MAN, on behalf of the Navy, undertook to create an S-boat engine as an in-line engine based on the principle of its double-acting 2-stroke engine.12 As an interlude, it must be mentioned here that even before this double-acting S-boat type, an attempt was made in 1930 in collaboration between the Navy and MAN to create an S-boat engine. A 10-cylinder 4-stroke engine (26/36) of around 1000 hp was developed, but it proved to be too heavy and bulky for S-boats. The six engines built were used for the small cruisers KÖLN, KARLSRUHE and KÖNIGSBERG, where they were subsequently installed as cruise engines with considerable difficulty. In 1933, MAN developed a new S-boat engine for the S-boats S 6 to S 9, initially a 7-cylinder engine with a cylinder diameter of 19 cm and a stroke of 30 cm (L7/19/30), which was particularly striking due to its slim and pleasing shape. The power achieved at 1050 rpm was 1300 hp. The weight was around 2 kg per hp. This type was followed by an 11-cylinder engine with the same dimensions. Its power was 2050 hp, and its speed, like the 7-cylinder, was 1050 rpm. Its auxiliary machines (flushing fan, cooling water and oil pump) were attached to the main engine and driven by gears with the interposition of elastic links. Although the detailed tests on the solid foundation of the test stand had fulfilled the expectations placed on the engine, it was unfortunately discovered during operation that this light engine did not prove itself due to the fact that, as a 2-stroke engine, mass balancing was not fully feasible. Its unavoidable vibrations led to cracks and breaks in the frame and to leaks in the oil, water and fuel lines. The lack of torsional rigidity of the frame caused the individual cylinders to make visible movements across the engine's longitudinal axis, which gave the impression of a serpentine line. As this meant that reliable and trouble-free operation was not possible in the long term, the construction of further engines of this type had to be abandoned after a series of this machine. Apart from that, its parts, such as cylinder glands or crossheads, gave no cause for complaint. The coupling to the propeller shaft was carried out by a constant velocity coupling, which allowed the running engine to be coupled to the running propeller shaft coupling. So the only S-boat engine left was the one from the Daimler-Benz works, which - as shown - achieved the desired result, although as a 4-stroke engine it was not exactly a simple engine in its construction. With regard to S-boat engines in general, it must also be mentioned here that the assembly of the boat engine systems was made considerably easier and simpler, as well as time and money saved, when the Navy switched to laying all of the pipes for this system as rubber hoses instead of copper and steel pipes. After the industry had made great progress in the manufacture of reliable hoses due to demands from the Air Force, a test could also be carried out on the speedboats, initially with some of the pipes. It was soon so successful that the entire pipe was then ordered to be laid as hoses. As far as I know, no difficulties arose with this hose pipe system.
Double-acting two-stroke engine of high power MAN
The development of the lightweight, double-acting, high-performance 2-stroke engine, which will be discussed below, was started by the Navy in 1927/1928, and the aim was to achieve weights of 6 to 8 kg/hp, while at that time the lightest engines of the same power rating weighed 5 to 10 times as much. This design represented a completely new development of the two-stroke engine, which was specially developed by the Navy with the MAN for the motor drive of warships. Only with this design could the Navy's requirements regarding space and weight requirements be met.
The intellectual father of MAN's marine diesel engine construction was Gustav Pielstick, who is one of the most important designers of the diesel engine.14 In addition to the MAN scavenging system, these engines also had a mechanically driven rotary valve mounted directly on the cylinders in the exhaust path, which served to maintain the scavenging pressure in the cylinder until the start of the compression stroke. The cylinder covers were replaced by steel cylinder covers, which also formed part of the piston running surface. The weight reduction achieved was achieved on the one hand by increasing the speed, but on the other hand the structural design of the individual parts also played a major role.
After the development of these engines was purposefully promoted by the Navy over the following years and had been pushed to the point where the installation of this type of engine was possible, the Navy commissioned the construction of an engine drive system for the small cruiser LEIPZIG, which was completed in 1931. The direct reason for this development was the project for the cruiser's cruise engine system. The Navy had to make demands on the weight of the mid-engine system that were considered almost impossible given the previous development of engine construction.15 For the engine alone, without gearbox and other accessories, a unit weight of only 5 to 6 kg was permitted. Since the power of an engine was to be calculated at around 3000 hp, this power could no longer be achieved with a single-acting four-stroke engine. Only the double-acting two-stroke engine design was an option. It was undoubtedly the most economical form in terms of the use of the engine. The reduction of the unit weight from 28 kg/hp for merchant ships and stationary systems to approximately 1/5 was an extraordinarily large leap. This first naval ship with a mixed steam and motor system was followed over the next few years by a series of identical and similar ship types, some of which had mixed propulsion (steam and diesel), but also purely motor propulsion.
Before we look at the engine itself, we will give a schematic representation of the engine systems of the small cruiser LEIPZIG, the artillery training ship BREMSE and the armoured ship DEUTSCHLAND and a list of the main specifications of the engines of these ships. The LEIPZIG had four double-acting seven-cylinder MAN engines of the type M7Z 30/4416 connected to a gearbox, each with 3100 hp at 600 rpm. Average piston speed 8.8 mm/s, average pressure 5.6 kp/cm2 for cruising speed.
For the main drive, the BREMSE had two sets of four two-stroke diesel engines of the MAN type M8Z 30/44, each with 3400 hp at 600 rpm. Average piston speed 8.8 mm/s, average pressure 5.3 kp/cm2 The main drive of the armored ship DEUTSCHLAND (from 1939 LÜTZOW) consisted of two sets of four MAN diesel engines of the M9Z 42/58 type with 7100 HP at 450 rpm. Average piston speed 8.7 mm/s, average pressure 5.2 kp/cm2.
Given the major leaps in development already mentioned and the relatively short time available, it is understandable that an engine that met all requirements could not be developed straight away. A number of improvements were therefore necessary at the beginning and over the following years, which arose from practical on-board operations. The BREMSE system that followed on the cruiser LEIPZIG and then the larger systems on the ironclads also underwent various innovations and improvements over the years based on the experience gained.
It is of course not possible to discuss all of these in their entirety. Only the most important and fundamental design measures that could be implemented on all engines due to their identical construction in all parts are given below.
Engine
In these highly developed, medium-speed, light engines, the engine is the most stressed part of the machine, and it was here that most of the problems occurred in the beginning, which led to design changes. Many years of operating experience have shown that the static strength values used in the design of the engine did not always offer the same level of safety as in conventional mechanical engineering. The stresses had to be set relatively high due to the low unit weight achieved. In conjunction with the high number of load cycles and speed, difficulties arose and investigations into the strength of building materials under high load cycles were necessary. This knowledge then inevitably led to a reduction in the specific stresses on the engine parts where their weakest points were. The later versions therefore have a lower specific stress. This made it possible to significantly increase the safety of the engine parts.
The additional weight caused by this was generally extremely low, so that it did not play a significant role in the overall weight of the system. For example, the stress in the piston rod, specifically in the lower thread, was reduced from 1150 kg in the first design for the cruiser LEIPZIG to 963 kg in the design for the cruiser NÜRNBERG and then in the subsequent systems to 925 kg per cm2. An even greater reduction in stress was achieved in the dangerous cross-section of the crosshead, where it was reduced from the original 1000 kg in the first design for the LEIPZIG to just 555 kg in the later systems. The vulnerable cross-sections in the drive rod were also strengthened in a similar way. It can be seen that attempts were made to reduce the stress in all important parts of the engine after it was seen that the stress in the first designs had exceeded the permissible limit somewhat, although this was not yet known at the time. With such a leap in the development of engine construction towards lightweight construction, it is inevitable that one has to feel one's way towards the actual goal.
Piston rod fastening in the crosshead and piston The most important and most stressed connection point of the engine was the fastening of the piston rod in the crosshead. The development of this point can be seen in a lecture I gave to the Shipbuilding Technical Society in 1938.17 The main development process is as follows: The piston rod was screwed into the crosshead using a nut with a double thread. It not only had to absorb the changing tensile and compressive forces resulting from the ignitions, but also, as later tests have shown, had to be able to withstand certain bending stresses. This resulted in a special form of this nut, the so-called
flexurally elastic crosshead nut. Over the years it has undergone a development that initially led to the "welded nut". The inner part of the nut was also provided with a recess, the purpose of which was to make the nut particularly elastic at this point and to deliberately place the crack at this point in the event of a break. The assumption was that if the nut broke at this point, the upper cracked part of the inner nut would rest on the collar of the outer nut, thus preventing the piston rod connection from completely separating. However, practice has shown that if the nut actually broke as a result of the impacts that then occurred, the collar in the outer nut could not withstand these stresses and separation still occurred. In addition, after several years of operation, cracks appeared at the welds between the outer and inner nuts, although these did not lead to the nut breaking. These nuts then became the "collar nut". But this design was not entirely satisfactory either, as it too showed cracks, although these were not dangerous as they did not lead to the connection breaking. Further development then led to a "one-piece nut". It was made from one piece and had an elastic, conical neck that provided the necessary bending elasticity. It was first installed on the ADMIRAL SCHEER ironclad. After it had proved itself there, it remained the final design. In order to reduce the notch effect of the piston rod thread as much as possible, this thread was designed as a round thread. The thread had a much greater rounding at the base of the thread than the normal thread. The fastening of the upper and lower parts of the piston to the piston rod also had to be changed over the years. In the first years of motor ships, there were no problems here. But after several years of operation, cracks appeared in the fastening between the upper part of the piston and the piston rod. The cracks did not result in any other damage to the engine or the cylinders, since during operation the ignition or compression pressure resting on the upper part of the piston prevented separation at this point. Only when the engine was stopped did separation occur because the piston cooling oil pressure pushed the upper part of the piston upwards and oil leaked out in large quantities. These breaks were all the more surprising because there are no tension-pressure changes at this point, only pressure, albeit a pressure that changes from 0 to a maximum. The only solution here was to significantly strengthen this connection by increasing the piston rod cross-section. The experience with this connection was quite satisfactory.
At the lower clamping point of the piston rod, tension-pressure changes occurred, which resulted from the ignition pressures, and also certain bending stresses, which came from the piston swinging back and forth in the cylinder within the piston clearance. The elastic design of the piston rod nut meant that these bending stresses could be made harmless for the nut. However, the piston rod cross-section was still highly stressed at this point.
Piston rod material
Since a significant reinforcement of the piston rod cross-section at this point would have resulted in a change in the dimensions of the crosshead nut, the crosshead, the stuffing box and also the lower cylinder cover, efforts were made to find a material that had a significantly higher fatigue strength in the notched state than all other types of steel instead of such redesigns. A steel with these properties was the nitriding steel, mainly manufactured by the Krupp company. Investigations into fatigue strength with this steel have shown extremely favorable results. While a tempered chromium-nickel steel only had a bending fatigue strength of 36 kg in the ground state, but only 28 kg in the notched state, the nitriding steel, in contrast, showed a fatigue strength of 60 kg, both in the ground and in the notched state. The notch effect therefore played no role at all here, which was of extremely great importance for machine parts that have to be connected to one another by threads. Due to these properties, all piston rods were made from this material and those that had already been installed were replaced with ones made from nitrided steel. The numerous tests and research showed that nitrided steel in its nitrided state was not surpassed by any other steel, no matter how high-quality, in terms of fatigue strength. The company therefore switched to making all highly stressed parts, including drive rod screws, crossheads, etc., from this material. By making piston rods from this material, an extremely important step was taken in terms of the operational reliability of this important component.
In order to further research the stresses prevailing in the clamping point of the piston rods, which cannot be fully determined by calculation, extremely interesting stress measurements were carried out on the piston rod of a running machine (ADMIRAL SCHEER). The tests were carried out by the State Materials Testing Office in Berlin-Dahlem under the direction of Dr. Ernst Lehr18, who unfortunately died far too early, and using an ingenious apparatus devised by him. In short, the result was that in addition to the basic load consisting of compressive and tensile stresses resulting from the ignition forces, bending stresses also occurred, which accounted for a considerable part of the basic stress and could lead to fatigue fractures of the piston rod. Another attempt was made to track down the stresses in the piston rod clamping point by subjecting the original engine parts to constant alternating stress. For this test, MAN developed a test device with which alternating stresses were generated by a pulsator made up of a number of rapidly rotating eccentric masses.
Research Institute for Mechanics and Design
These investigations provided such valuable findings that, at the suggestion of Heinrich Waas, the Navy saw fit to set up a test facility at MAN in Augsburg under the direction of Ernst Lehr, in which dynamic strength tests of this kind could be carried out, on original machine parts up to the largest dimensions. This "Research Institute for Mechanics and Design" was probably the largest and best equipped institute of its kind at the time.
The institute cost 3,591,000 RM, of which the German Navy paid 85% = 3,052,000 RM. Its facilities were completely dismantled by the American occupying forces and sent to America.
Crankshaft
The last of the engine parts is the crankshafts, which were of course designed to withstand the normal stresses caused by torque and piston forces with the necessary safety. Even if the crankshafts were calculated in terms of vibration, critical areas could not be avoided. These areas should have been closed off during on-board operation! However, since such restricted areas are not acceptable for warships, ways and means had to be found to dampen these critical areas to such an extent that driving in them was possible without excessive stress on the crankshafts.
Vibration damper
The means of achieving this damping was the vibration damper. After testing various systems (rubber vibration damper, hydrostatic vibration damper and mercury vibration damper), the sleeve spring vibration damper developed by MAN proved to be the most effective.19 The principle of the sleeve spring damper was that a flywheel mass is attached to the free end of the crankshaft, where the deflections are greatest, and is elastically coupled to the shaft by specially designed springs. The shape of the springs is chosen in such a way that not only a springy connection is created, but at the same time a strong damping is exerted so that "rocking" does not occur. After the operational safety
and good effect of this damper design was recognized, all Navy engines were equipped with it. The same principle as for the dampers could also be used to great advantage for flexible couplings, for example when coupling the engine with a gear transmission, where it is generally necessary to insert an elastic intermediate gear in order to keep the irregularities in the crankshaft torque and small torsional-critical vibrations away from the gear transmission. The sleeve spring coupling has proven to be very effective for this purpose in all systems. By using sleeve spring vibration dampers and sleeve spring couplings, it was possible 1. to avoid any dangerous critical stress in the crankshaft, regardless of how many cylinders the engine had, and 2. to derive a completely uniform torque from the clutch side, so that a gear transmission could be coupled without any problems.
If crankshaft breakages or cracks in the crankshafts did occur in some systems, this was due to the fact that these systems were initially equipped with dampers that were insufficiently effective. For example, a crankshaft fracture occurred on the LEIPZIG, the cause of which could not be fully determined, however, as in addition to the critical stresses, corrosion inside the crankshaft bore may have played a significant role. This corrosion was caused by lubricating oil containing seawater. Cracks were also discovered in the crankshafts of the engines of the artillery training boat BREMSE, which originated in the lubrication holes and could be clearly identified as torsional cracks.
These cracks undoubtedly occurred at a time when the engines were still equipped with hydrostatic dampers, which occasionally failed and thus caused very high additional stresses in the crankshaft.
In principle, it can be said that after the development of the sleeve spring damper and the sleeve spring clutch, every engine system could be built in such a way that dangerous critical stresses on the shafts no longer occurred and the engine could be operated across the entire speed range.
This would essentially list the experiences gained with the engine components and the resulting improvements. A few words remain to be said about the changes to the frames, cylinders, etc. The other structural components of these double-acting 2-stroke engines have proven to be fully operational. No damage that could be attributed to fundamental errors has occurred.
Cylinders: Cylinder center pieces and cylinder screws
Only the design of the cylinder center pieces had some weaknesses, so that over a longer period of operation cracks and thus water leaks appeared. New cylinder center pieces were therefore reinforced at the vulnerable points and those already installed were replaced by reinforced ones. A later significant improvement in the design of the cylinders should be mentioned here: This was the wave-shaped joint between the cylinder center piece and the cylinder covers. This wave-shaped transition is much more favorable for the piston rings to run than the straight joint as was initially used. The advantage was that the number of piston ring breaks, which initially occurred in large numbers, has since decreased significantly.
In order to reduce wear on the cylinders, the cylinder running surfaces were hard chrome-plated. This measure was quite successful. Since then, wear has hardly been noticeable; it was only a small fraction of that of the non-chrome-plated cylinders. The surfaces of the steel cylinder barrels were also galvanized, and those of the steel cylinder screws were parkerized.20 The transfer of the forces from the tie rods to the fastening of the cylinder covers also proved to be unfavourable. The ribbing
was reinforced or relocated more favourably. Since no damage occurred later on to these parts, it can be assumed with good reason that the new design was able to withstand all stresses.
Since the seawater cooling initially chosen for the engines led to intolerable corrosion phenomena, freshwater cooling was used for the later systems.
Welded engine frames
An incident on the BREMSE led to the use of welded engine frames instead of cast ones, as used on the LEIPZIG and BREMSE systems. On the BREMSE, an engine had broken through and been completely destroyed due to the failure of the safety regulator against over-revving.
It looked as if it had collapsed. Strangely, no parts had flown out, as one would have expected in such a case. None of the personnel standing next to the engine had been injured. The reason for the failure of the safety regulator has not been fully explained. The
rods to the regulator must have been bent for some inexplicable reason, so that the regulator could not operate.
The welded construction offered the advantage of absolute safety in production, as there was no risk of any foundry-related errors. Another advantage was that if the frames were damaged in any way due to engine breakage or similar, they could be repaired, which is generally not the case with cast frames. Just think of a hit in the engine room! Another advantage is that welded structures are significantly lighter than cast ones and can also be manufactured more quickly.
Vibration damper
The nature of the piston engine means that free forces or free moments or vibrations are noticeable in the engines in question due to the masses moving back and forth and rotating. While it is usually possible to compensate for the forces and moments of a lower order structurally, this is not completely possible with higher orders. In general, these forces are absorbed by the rigidity of the engine itself or the ship's foundation. There are engines with a number of cylinders and crank arrangements in which such mass moments are relatively large and which then lead to heavy stress on the engine frame and the ship's foundation and can ultimately cause cracks to form.
One such case was the auxiliary engines of the ironclad DEUTSCHLAND, which, as five-cylinder engines, had relatively large mass moments. After a long period of operation, cracks appeared in the frame and the ship's foundation. It should be stressed, however, that the design of the ship's foundations could not be considered particularly practical according to later findings. It was therefore necessary to significantly strengthen these parts of the ship and to provide a better connection between the foundations and the other parts of the ship. In addition, the free mass moments of the five-cylinder auxiliary engines were eliminated by means of a mass balancing gear. The effect of such a gear is based on the fact that rotating masses are attached to both ends of the engine, which generate mass forces or mass moments that are opposite to those generated by the machine, thus making it possible to achieve complete balance.
Engines with attached auxiliary machinery
The engine systems that were built later than those for the DEUTSCHLAND class (they were those for the submarine and S-boat escort ships) are particularly noteworthy because, apart from the MAN S-boat engines, they were the first to use engines with attached fans and pumps. On the earlier ships, these auxiliary machinery had a special drive motor that drove the following auxiliary pumps on all ships:
1. Fan;
2. Oil pump for piston cooling and lubrication;
3. Sea water pump;
4. Fuel feed pump;
5. Leakage oil pump for the Vulcan coupling21 (this pump serves to replace leakage losses when the clutch is engaged);
6. Maneuvering oil pump (can be uncoupled using a special small Vulcan coupling). This pump was used to fill the actual Vulcan couplings and was only engaged when maneuvers were imminent in order to save power.
These auxiliary engines were no longer required in these systems. The attached auxiliary machines made the systems extremely clear and simple. Since all cross-connections between the main engines and auxiliary engines were eliminated, the space and the bilge were significantly less crowded, in contrast to the ironclads, which still suffered from a large tangle of pipes.
Lubricating oil and lubricating oil cells
It should also be noted that the amount of lubricating oil in circulation could be kept significantly lower than on earlier ships, as each engine had its own oil pan.
The space gained in double bottom cells could be used for fuel and lubricating oil supplies. Furthermore, these systems were the first to feature a strict separation of the lubricating oil used for the engines and for the Vulcan gears, in order to avoid the excessive foaming of the lubricating oil, which was mainly caused by the gears and Vulcan clutches.
Improvements to the engine frame
The engine frames of these ships were also improved, if not fundamentally, then in some respects compared to the DEUTSCHLAND version based on the experience gained so far. The main change related to increasing the rigidity of the frame in the vertical direction. Previously, the slideways and the large side casing covers were only attached to the vertical anchor columns and did not contribute to stiffening the frame. The new slideways and casing covers were designed in such a way that they were used to stiffen the frame and also to increase the strength in the longitudinal direction. In order to transfer the forces to be absorbed by the foundation bolts to the frame with as little bending stress as possible, the holes for the foundation bolts were brought very close to the side wall of the frame. The main innovation in these engines concerned, as already mentioned, the attachment and drive of the attached auxiliary machines, which had been carried out for the first time on speedboat engines and had proven to be very successful. This simplification could now also be applied to the much larger engines.
Attached auxiliary machines
As the power of the driven auxiliary machines is quite considerable, around 20% of the nominal power of the actual machine, very special care had to be taken in the design of the drive. In order to keep the drive free of any vibrations and irregularities in the torque, the drive wheel on the crankshaft was designed to be elastic in the form of a sleeve spring coupling. The fan pinion was then driven via an intermediate wheel with a ratio of around 1:10 at around 4000 rpm. The use of turbo blowers for the pre-compression of the scavenging air was new, in contrast to the compression with piston characteristics otherwise usual in 2-stroke engines. The pump shaft was then also driven via an intermediate wheel at around n = 3000 rpm to the side of the large drive wheel. The control shaft and reloading slide were also supported in a similar way by an intermediate wheel.
The difficulties with the turbo blower mentioned above were primarily that sufficient air power had to be provided even when running backwards. This was not possible with a normal spiral housing and an impeller that was only built for "forward" travel. Extensive tests then led to the construction of a blower that, thanks to the special shape of its spiral housing, still provided sufficient pressure and volume even when running backwards to ensure sufficient reverse power for the engine. The spiral housing was widened at the side by an attached channel. This made it possible to significantly improve the characteristics of the blower when running backwards. The tests on the test bench then showed that despite the significantly lower
Due to the air output of the blower when reversing, it was possible to drive with about 80% of the torque, at least at high speeds. This should have been sufficient in all cases. The seawater and freshwater pumps built by the Kleinschanzlin-Bestenbostel company in Bremen22 are also notable for having to be specially designed for reversing. Here, by positioning the impeller blades accordingly and by using two guide wheels and two spiral casings, it was possible to keep the pump characteristics the same for forward and backward. As it became apparent that the use of centrifugal pumps for oil extraction in ship systems had certain disadvantages, it became necessary to arrange a special feed pump for each oil pump, which fed the oil to the actual feed pump at an excess pressure. As this feed pump would also have had to be driven, either electrically or hydraulically, this resulted in considerable complications. To avoid this complication, displacement pumps were chosen for oil pumping in the new systems, including the very large engines (MZ 65/95) that will be mentioned later. The most suitable type of pump was the screw pump from Leistritz in Nuremberg. The pumps were completely silent and were also insensitive to oil containing air. They were also able to overcome a relatively high suction head safely, even with oil containing air. The pump was made reversible by installing valve flaps.